Understanding how productive, efficient, and profitable your business operations
One of the tools used in manufacturing, automation, and process control to stay on top of these metrics
KPIs can be applied to all levels of a business, from manufacturing to sales, marketing, operations, and customer service.
So what’s a KPI? As Klipfolio describes it, a KPI is "a measurable value that demonstrates how effectively a company is achieving key business objectives.
"Organizations use KPIs at many levels to evaluate the success of reaching target goals. High-level KPIs may focus on the overall performance of the enterprise, while low-level KPIs may focus on processes in specific departments," such as manufacturing output.
Developing KPIs
When developing KPIs for your organization or process, here are some important ideas to keep in mind.
Focus on the most important indicators. For example,
Develop your KPIs as part of your overall business strategy. Remember that the objective of a KPI is not just to measure overall performance, but to measure progress toward a performance goal. For example, you may set a goal of lowering raw material cost by 3% over the next 3 months; your KPI measures progress toward that goal. And remember that the KPIs you develop should measure the most critical factors in achieving your organization’s or department’s success.
Make sure KPIs are easy to understand at all levels of the department or organization. To reach goals, your team members need to understand what the KPI indicates and why the KPI is in place. A good framework to achieve this is to apply the SMART principle, which states that goals should be specific, measurable, attainable, realistic, and
Verify that the data used to generate KPIs is correct. One of the first steps in process improvement is to make sure you’re working with good data. Your litmus test should be whether or not the system you’re using to generate your KPI data will yield information that is meaningful, timely, and reliable for making sound management decisions. Always remember to validate the repeatability and reproducibility of your measuring system.
KPIs for Manufacturing Processes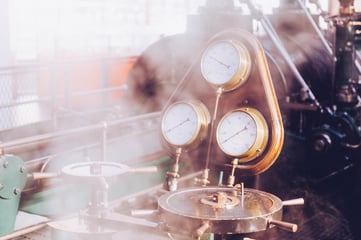
Here are ten KPIs you might consider implementing in your manufacturing process to help achieve an overall picture of performance.
Remember that your KPIs should be designed to fit your specific goals for improvement and progress towards that improvement.
Total Output—This is the total number of units produced, including good units and bad units. Total output helps you keep track of revenue, production costs, and profit.
Good Unit Count—Knowing how many defect-free products you produce is an important metric for the organization. For example, it can be used to keep the sales department informed on how many units are in inventory and ready to ship to customers. It also gives an overall indication of how well a manufacturing line is running.
Bad Unit Count—Keeping track of the number of defective units produced (and exactly where and how they were produced) can help pinpoint problems in a manufacturing line or process. A high number of bad units produced indicates that there may be a problem somewhere in the manufacturing process, the machinery used on the manufacturing line, or the raw materials sourced for manufacturing.
Equipment Availability—Availability takes into account unplanned and planned stops. An availability score of 100% means the process is always running during planned production time.
Number of Unplanned Stops—This KPI indicates the number of times production stops unexpectedly, for
Number of Planned Stops—Planned stops indicates the number of times the production line is brought down for maintenance, upgrades, and so on. It can be a good indication of how well your manufacturing equipment is running.
Slow Production Cycles—These are production cycles that take longer than the ideal production cycle but not as long as a full production stop. Slow production cycles can add up, leading to decreased overall manufacturing efficiency.
Small Production Stops—Small production stops occur when there’s a pause in production, but it’s not long enough for the manufacturing line to actually be considered down. Small stops can add up, too.
Rework Count—Indicates the number of units that did not have to be scrapped but did require repair or component replacement before being shipped to a customer.
OEE—Finally, OEE stands for overall equipment effectiveness and takes many of the KPIs above into account. To find OEE you would multiply availability by
Additional Information
Need more information on developing KPIs to reduce downtime? Check out the ebook from AutomationWorld.com.
Need an easy way to display KPIs on big-screen TVs throughout your plant, or keep track of them wherever you are with your mobile phone? Check out the