Opto 22 knows solid-state relays (SSRs) very, very well. We’ve been manufacturing our optically isolated, epoxy-filled SSRs for more than 40 years, and over that time have gained quite a bit of practical knowledge and experience about using SSRs in applications.
SSRs have replaced electromechanical relays (EMRs) in many applications, thanks to their advantages:
- long service life
- low noise generation
- compact size
- no moving parts
- total absence of arcing
These advantages make SSRs ideal for applications involving repetitive operations or fast turn-on/turn-off times, or in areas where you need minimal electrical noise.
Two factors inherent to semiconductor-based relays—leakage current and operational temperature limits—require some attention when you use SSRs.
Leakage current. When in the “off” state, an SSR will exhibit a small amount of leakage current, typically a few mA. It's slight, but this current can keep some loads from turning off, especially ones with a high impedance like a small solenoid or a neon lamp, which have relatively small “hold in” currents.
For SSRs that switch high voltages, leakage current can also cause circuits with SSRs that are switched off (electrically open) to still have potentially troublesome voltages on the outputs. Usually you can address these issues by placing a power resistor, sized for 8-10 times the rated maximum leakage current for the SSR, in parallel with the load.
Operational temperature limits. Semiconductor-based relays become less efficient as the relay temperature increases, so the current rating for an SSR is de-rated, or reduced, based on the ambient temperature. An SSR also generates heat in the “on” position, so heat management is vital.
To combat heat, be sure to use an appropriate heat sink for your SSR, and put a small amount of thermal grease between the base of the SSR and the heat sink. Also make sure to review the SSR de-rating curve (see an example on this page) in the SSR data sheet so you know what to expect.
Selecting a relay for your application
Here are a few guidelines to keep in mind when selecting a relay for your application. See the resources listed afterwards for more information and other considerations.
Use an SSR if your application requires:
- Repetitive operation cycles, like lights and electric heaters—SSRs have no mechanical components to wear out, and have no failure mode related to the number of cycles of operation.
- Minimal electrical noise—SSRs greatly minimize electrical noise because they turn on and turn off when voltage is zero in the AC cycle. Most EMRs turn on and off at any point in the AC cycle, so they can generate significant electrical voltage spikes, causing electrical noise that can affect other devices in the area.
- High-speed timing—SSR turn-on times are highly predictable, while times for a mechanical relay vary based on the nature of the device and the environment.
Consider an EMR if your application requires:
- High starting loads, such as motors and transformers—SSRs are more sensitive to voltage transients than EMRs, even SSRs with good transient protection (like Opto 22’s), and if a relay gets hit hard enough a sufficient number of times, it will degrade or fail. This makes SSRs less ideal for driving highly inductive electromechanical loads, such as some solenoids or motors.
- Operation in high-temperature environments—SSRs become less efficient as the relay temperature rises, and the current rating for an SSR is de-rated, or reduced, based on the ambient temperature. EMRs are not affected in the same way.
- Zero leakage current—In the “off” state, an SSR will exhibit a small amount of leakage current—typically a few mA. EMRs do not exhibit this leakage current due to their mechanical operation.
More information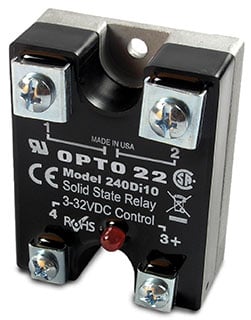
Opto 22 Solid-State Relays (SSR) datasheet
Guide to Troubleshooting Legacy Opto 22 Products
SSR series and manufacturer part number cross-reference list