Over the years, one of the most difficult things I’ve had to help clients with is justifying an automation project. Whether it’s a new system or an upgrade, the challenge is often in quantifying the benefits financially.
Return on Investment (ROI) is typically the measure used to justify capital expenditures. And ROI is often defined by the period of time (months or years) it takes until the financial gains offset the investment.
ROI challenges in automation
In industrial automation, I see two main challenges:
- ROI is often a chicken-and-egg scenario: some of the gains from the project may not be apparent until the project is finished, or at least until it’s started and opportunities reveal themselves.
- Another factor can be inertia, or an “if it isn’t broken, don’t fix it” mentality. I can certainly empathize with operators or plant engineers not welcoming significant disruptions in their work lives!
I’ll share a few thoughts on each of these two issues, and would welcome yours as well.
The chicken and the egg
For an ROI analysis, the first step is of course to understand current costs, and then segue to improvements that automation could bring. It helps to use your imagination here and look long term. What could happen if you add or change capabilities for monitoring, control, or acquiring data?
Think about these examples of potential improvements, and you’ll probably come up with some others, as well:
- Reduced labor costs
- Reduced product reject rate
- Improved cycle time
- Reduced downtime
- Increased consistency of product quality
- Reduced costs associated with safety improvements
- Reduced energy consumption
Once you’ve identified expected improvements like these, associating dollar values with them can still be difficult.
In my experience, the people responsible for the process, machine, or plant floor may have KPIs (key performance indicators) related to production that are not tied to financial metrics. But this problem can be solved with a bit of thought, effort, and cooperation with the Accounting Department.
Things are running fine
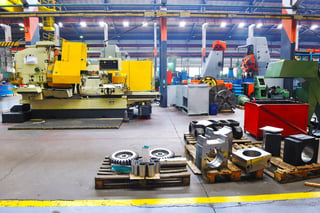
In justifying upgrades, the motivation is obvious when the frequency of failures increases, parts are no longer available or costs rise, or when obsolete technology causes interoperability problems.
Justification is less obvious when “things are running fine”—or at least they appear to be.
Why fix it if it doesn’t look broken?
Here at Opto 22 our pre-sales application engineers get calls and emails every week from people who have inherited a system from someone who is no longer there, or people whose systems were installed by a System Integrator who is no longer accessible. The system was initially configured and has been running ever since, but now a change needs to be made or something isn’t quite right.
What is often uncovered is that things like the control scheme, set points, or PID loop tuning were either not optimal from the beginning or do not reflect conditions that have changed over time.
Hidden costs and benefits
Some ROI factors are hidden, but they are still important things to consider when doing an ROI analysis for industrial automation. Here are two of them.
The first is Total Cost of Ownership (TCO). Initial costs include the obvious things, like hardware, software, labor and parts for installation, and programming. But TCO includes longer term costs, such as software licenses, ongoing training, and product upgrades. These can really add up over time and should be factored into ROI.
The second is identifying intangible benefits, which may be difficult to trace to dollar values but are benefits or gains nonetheless. One example might be an employee not having to stay late or check on systems over the weekend. Another might be the ability to focus on other areas of the business, due to more free time facilitated by automation.
The IIoT makes justification easier
One thing that is making it increasingly easier to justify automation is the proliferation of the Industrial Internet of Things (IIoT). IIoT projects typically start with a business issue that needs to be addressed, which means the origin is often financial in nature.
The promise of the IIoT is the benefits that can be gained from data transfer and analysis. Lots of cloud services and platforms are out there now from IT companies like IBM®, Microsoft®, SAP®, and others. They are designed to ingest data from multiple sources and perform advanced analytics.
The result is data you can use to achieve measurable business results.
This is good news for automation project justification, because one of the main sources of industrial data will of course be automation systems and equipment. Legacy systems contain a wealth of useful data that’s not currently accessible for this kind of analysis, but some newer control products can make this data available with little or no impact on functioning equipment.
Our SNAP PACs and groov® are good examples. These controllers and appliances combine industrial reliability with support for standard IIoT protocols, data formats, and tools like RESTful APIs, MQTT, JSON, and Node-RED.
What do you think?
How do you justify new automation projects? Perhaps you have favorite formulas for presenting benefits or thinking through costs. Please feel free to share your experiences, ideas, and thoughts in the comments. I’d love to hear from you.